AM Business Development Ltd.

Nitruration Heat Treatment
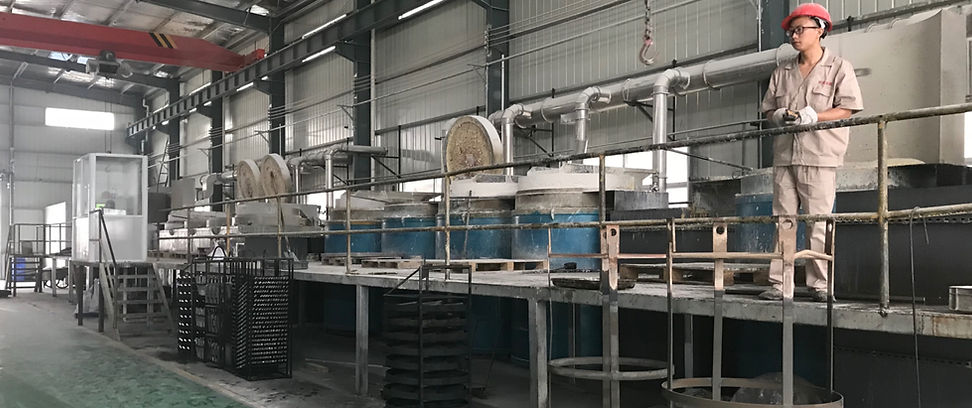
The SIMT nitruration process (Also knowns as nitrucarburation or Quench-Polish-Quench) is a process in which the surface of the steel goes through a series of salt baths and polishing, providing high surface hardness and corrosion resistance, without causing any deformation to the treated part.

Characteristics

The SIMT process is targeted at treating ferritic alloys, such as carbon steel, structural alloy steel, tool steels, cast irons, and other ferritic alloys. It has the capacity to provide improved surface hardness, wear resistance, corrosion resistance and fatigue resistance. Its relatively low process temperature also provides de advance of no deformation, which could be critical for parts with complex geometry or which are difficult to straighten afterwards.
Advantages of the SIMT Nitruration
Increased wear and fatigue resistance

After nitruration, the material forms a complex carbide layer on the treat surface, which increases the hardness of the part, making it more resistant to wear, and reducing the probability of parts failing due to fatigue because of its increased hardness.
High Corrosion Resistance
The salt bath nitruration process forms a layer of complex carbides which prevents the material from interacting with the oxygen and other corroding agents. Salt spray tests have shown that the start of corrosion on nitruration treated carbon steels is four times longer than for nickel-chrome steels, which are also more expensive, and have lower mechanical properties.
Almost No Deformation of the Workpiece
Nitruration has the advantage that the workpiece suffers almost no deformation. This presents a clear advantage when hardness and dimensional accuracy are critical. For example: shafts, slender bar parts, rotation axles, piston rods, and parts with complicated geometries.
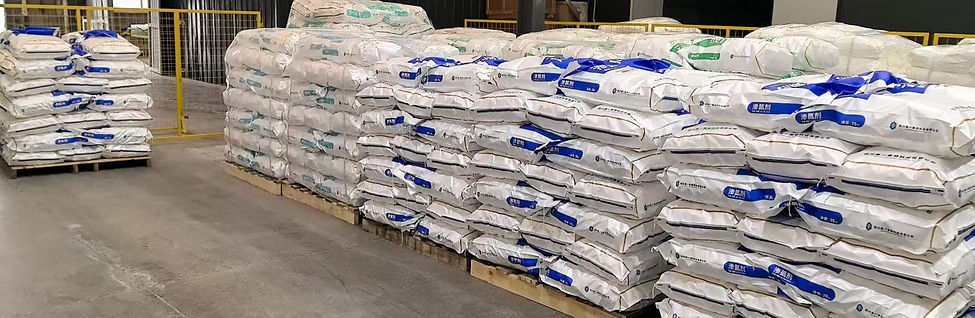
Applications


Agricultural Industry
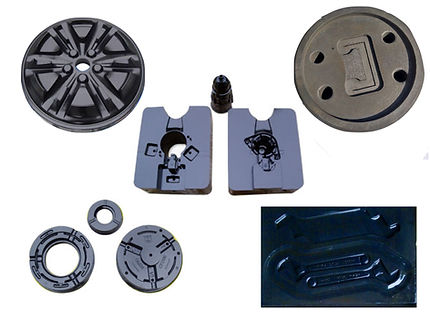
Tooling: Die casting, Investment Casting, Precision Forging, Aluminum Extrusion

Oil&Gas Applications

Automotive
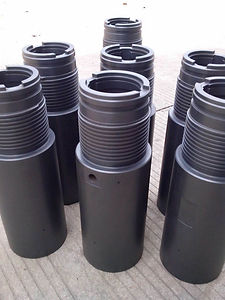

